Powder Compaction Solutions
Cold Isostatic Presses
Powder Compaction Solutions
Powder compaction is the process of compressing metal powder in a die by applying high pressures. This compression molding technique typically involves using a press to condense the powder into complex shapes from powder compounds like metallic, composite and ceramic to create functional and structurally sound metal parts.
Gasbarre Products, Inc. offers a full range of powder compaction and sizing solutions for a full range of applications. Gasbarre has decades of press building experience, offering standard and custom equipment solutions. Auxiliary equipment and worldwide support mean that Gasbarre will be with you throughout the life of your press.
Gasbarre’s products and services include amongst others:
- Start-to-finish Equipment
- Development and Manufacturing Projects
- Design & Maintenance of Presses
- Spare Parts & Tooling
- Machine Upgrades
The Gasbarre Family:
- Simac Ltd.
- PTX-Pentronix
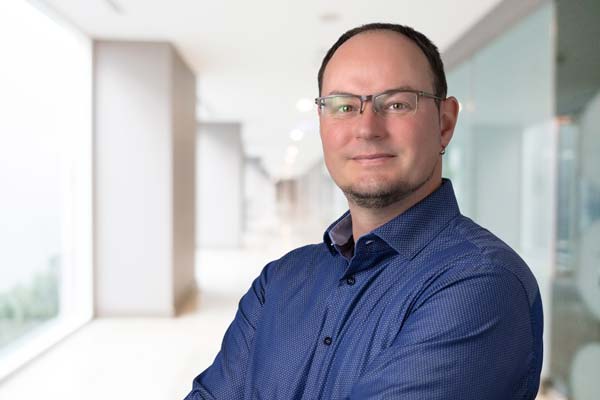
Steve Urbanczyk
Ask me for more information.
+49 (0) 2244 918 130
Isostatic Press Solutions
At Gasbarre, we produce isostatic presses that make powder compaction easier and more efficient than ever.
Our state of the art isostatic press, featuring a fully automatic ‘lights out’ cycle to mass produce rods, tubes, and balls.
What Are Isostatic Presses?
Isostatic pressing is a process involving the application of equal pressure to a compacted powder to achieve optimal density and microstructure uniformity. Through this process, the press uses a gas or liquid to deliver force to a hermetically sealed container filled with the metal powder using either elevated or ambient temperatures. These processes are known as hot and cold isostatic pressing, respectively.
What Is Cold Isostatic Pressing?
Gasbarre isostatic presses are optimized for reliable cold dry bag isostatic pressing. Cold isostatic pressing involves the compaction of powders encased in elastomer molds.
Through this process, the mold is placed into a pressure chamber and filled with a room-temperature liquid before the press applies the pressure from all sides, condensing the metal powder. As a result, the powder particles mechanically bond to each other, creating a solid green body. Finally, the liquid is removed and the container expands to its original form so that the product can be retrieved.
There are two types of presses used for cold dry bag isostatic pressing — monostatic isostatic presses with single-cavity structures and densomatic isostatic presses with multi-cavity designs.
Our Isostatic Presses for Powder Compaction
We carry reliable and innovative cold dry bag isostatic presses for powder compaction. Gasbarre’s SIMAC product line offers uniquely configured presses to allow for the laboratory or production manufacture of uniform density components. The dry bag design simplifies powder filling, compaction and ejection and is more efficient, allowing for quick, ready-to-press parts.
SIMAC presses include a tool mounting system that allows for a wide range of parts to be produced in the same machine. Their dual inner bag configuration allows simple tool changeover.
Monostatic Isostatic Presses
Our monostatic presses comprise a single-cavity design suitable for research and development (R&D) as well as production needs. Our automation systems and in-line horizontal lathes are available add-ons. Gasbarre monostatic presses comprise the following characteristics:
- SINGLE CAVITY
- SEMI OR FULLY AUTOMATIC
- ADJUSTABLE DWELL
- BUILT TO FIT APPLICATION
Some of the key features of our monostatic presses include:
- Removable inner (product) tools.
- Manual or semi-automatic operation.
- Adjustable iso-pressure.
- Certified pressure vessels.
- Bottom part removal.
- Part ejection elevator.
- PLC control with Graphical User Interface (HMI).
- Iso-pressure monitoring via electronic transducer.
- Adjustable iso-pressure.
- Fully enclosed service-ready pressure panel.
Densomatic Isostatic Presses
Our high-speed, automatic, multi-cavity machines are capable of producing a wide range of components at pressures up to 2100 BAR. Gasbarre densomatic presses are ideal for the manufacturing of spark plug insulators, oxygen sensors and grinding media. In-line profile grinders and automatic loaders are available to improve production efficiency.
Our densomatic presses have all of the following traits:
- High volume
- Range from 5-150 T
- Contain up to six cavities
- Bottom or top ejection
Gasbarre densomatic isostatic presses are suitable for many applications, including:
- Spark plug insulators.
- Balls.
- Lamp tubes.
- Drill banks.
- Rods.
- Spray nozzles.
- Sensor bodies.
Benefits of Isostatic Presses for Powder Compaction
Cold isostatic pressing comes with many advantages that will optimize your metal powder compaction processes, such as:
- Predictable shrinkage during sintering.
- Reduced production costs.
- Ability to produce large parts with uniform densities.
- High green strength.
- Flexibility to create hard-to-produce shapes and dimensions.
Why Choose Gasbarre for Isostatic Presses?
Gasbarre has delivered strong and dependable manufacturing equipment and services for over 45 years, and we continue to maintain our positive reputation today.
As a family-owned business, we put our customers first. That’s why we perform services with the life of the equipment in mind instead of phasing out products to push new machine sales. If you have an urgent equipment servicing need, you can expect our team to get the job done.
SIMAC Series V Monostatic Press - Automatic Pressing
SIMAC Series V Monostatic Press – Automatic Pressing
When it has to be efficient, it has to be Gasbarre!
Gasbarre’s state of the art isostatic press, featuring a fully automatic ‘lights out’ cycle to mass produce rods, tubes, and balls.
Key Features:
- Fast Cycle Rate: 48 Second Cycle
Almost 2x faster than previous models - Dry Bag CIP Design
Simplifies the cycle and allows for clean changeover. - Versatile Tool Envelop
Allows for fill diameter up to 50mm and length up to 500mm. - Electronic Powder Weighing System
Accurate to 0.01g. - Intuitive HMI
Creates an easy platform for new part development and quick changeover.
Maintenance alerts, alarms and production tracking/tracing
Whether for laboratory or production, Gasbarre’s SIMAC product line fits your needs by offering uniquely configures presses to produce uniform density components. The dry bag design simplifies powder filling, compaction, and ejection and is more efficient allowing for quick changeover of application tools.
SIMAC presses include a tool mounting system that allows for a wide range of parts to be produced in the same machine. Dual inner bag configuration allows simple tool changeover.
Let Gasbarre become your trusted partner.
Whether you’re looking for densomatic or monostatic presses, Gasbarre has the state-of-the-art solutions you need. We design machinery that’s built to last with around 50 years of dependable service.
For more information on our products, call +49 2244 91813 0 or contact us online today!
Uniaxial Press Solutions
We manufacture uniaxial presses with the following base technologies:
Mechanical Powder Press
A full range of powder compaction and sizing solutions for a full range of applications. Gasbarre has decades of press building experience, offering standard and custom equipment solutions for customer challenges. Auxiliary equipment and worldwide support mean that Gasbarre will be with you throughout the life of your press.
View Gasbarre’s Mechanical Press Brochure
What Are Mechanical Presses?
Mechanical powder presses condense powders in the powder metallurgy process. Any machine that exerts pressure without the use of hydraulics to shape, form or cut materials, compress solids or extract liquids is considered a mechanical press. This equipment is used for manufacturing metal parts, sheet metal working, technical ceramics production and other metal forging applications.
How Does a Mechanical Press Work?
Mechanical presses use rotational force from the motor and convert it to a translational force vector that aids in pressing. They can be single-, double- or triple-acting, depending on how many rams are present.
To operate, the machine’s electric motor creates power and transports it to the flywheel. After being initiated by the clutch and brake, the motor drives a gear train that channels the energy to the crankshaft, which moves the press slide vertically. Then, the motor reinstates power to the flywheel, beginning the process again.
Types of Mechanical Presses We Offer
If you’re looking to optimize your powder metallurgy processes, Gasbarre has numerous types of mechanical presses you can choose from based on your individualized needs. All of our mechanical powder presses have their own specialized components, features and functions — because no two metalworking jobs are exactly the same.
Performance Series
Our performance series presses are the affordable solution for single- to multi-level parts.
Die Set Series
Our die set series mechanical powder presses are ideal for multi-level parts and applications requiring a removable die set.
Multi-Action Series
The multi-action press series from Gasbarre is one of our biggest and best yet. This state-of-the-art technology is designed for complex, multi-level part construction.
PTX High-Speed Powder Compaction Presses
A complete line of high-speed and high-precision powder compacting presses, robotic parts loaders.
Custom Mechanical Presses
We offer custom fabrication options where our team of skilled and knowledgeable associates will work with you to create a solution designed to meet your unique needs and incorporate seamlessly into our company’s processes. Our comprehensive range of fabrication capabilities allows us to develop custom machines individualized to your needs.
CNC Servo Hydraulic Press
Our cnc hydraulic presses are manufactured in capacities from 15 tons to 1,200 tons for single-level or multi-level parts for carbides, ceramics, powder metals, polymers and other particulate material industries. Gasbarre’s computer numerical control (CNC) hydraulic presses are optimized for reliable and lasting service with numerous innovative features and application capabilities.
What Are Servo Hydraulic Presses?
Hydraulic presses use hydraulic cylinders to produce a compressive force that aids in lifting and condensing large items. This equipment is optimized to perform various actions, including stamping, molding, punching, forging, clinching, metal and rubber formation, and powder compacting.
CNC hydraulic presses play a role in numerous industrial applications, such as ceramics, car parts, aircraft, appliance and electrical component manufacturing.
How Do Hydraulic Presses Work?
Hydraulic presses operate on the principle of Pascal’s Law, which states that when pressure is applied to a confined fluid, it transmits that force across the entire solution, resulting in the same pressure change throughout.
These machines are powered by manual, electric or pneumatic pumps and generate a fixed pressure that expands the cylinders. Hydraulic presses comprise two fluid-filled cylinders — a large one, known as the ram, and a small one, known as the plunger. The press operates by exerting force onto the plunger, which reacts by pressing the fluid beneath it. Then, the pressure evenly distributes and raises the ram. Once the pressure is dispersed between both cylinders, they work to condense the item placed between them.
Benefits of Using Hydraulic Presses
Using servo hydraulic presses in your automotive manufacturing facility means experiencing all the benefits of these powerful and reliable machines, including:
- Greater pressure, travel distance and position control.
- Minimal maintenance and repairs.
- Easily replaceable parts.
- Overload protection capabilities.
- Quiet operation.
- Smaller surface area for better space savings.
Why Choose Gasbarre for CNC Hydraulic Presses?
Our family-owned business has provided auto manufacturers with reliable powder compaction solutions, thermal processing systems and manufacturing technologies since our establishment in 1973. We set ourselves apart by servicing machines for the life of the equipment, maintaining our products without pushing customers into purchasing our newest solutions by discontinuing our old ones. When you choose Gasbarre for hydraulic presses, we’ll deliver the assistance you need, no matter the day.
Electric Powder Presses
The Gasbarre electric press provides precise compaction of powder into a wide variety of geometries. High-efficiency and high-precision drives control the motion of the upper ram, die plate and automatic die filling systems. Each axis of the press is freely programmable for complete control of the compaction cycle, die filling, upper punch motion/compaction, die motion and ejection cycle. Movement of the press axes is performed by closed-loop control. Extreme precision and repeatability are the results.
What Are Electric Presses?
Electric powder presses are servo-powered equipment designed for compressing materials under high pressures. Because of their servo motors, these machines can control the output shaft’s positioning and speed rather than maintaining a fixed press cycle speed. Electric metal presses also use a closed looping feedback system to enable more precise cycle rate and load regulation and can perform all of the following functions:
- Inserting
- Clamping
- Press fitting
- Riveting
- Staking
- Crimping
- Joining
- Punching
- Swaging
- Spring testing
How Do Electric Powder Presses Work?
Like most presses, electric powder compaction presses operate by pressing a die or plate against a material using high pressures to deform it. Servo presses locate and deliver the product by pushing the upper or lower die or plate onto the piece using primarily hydraulic pressure.
Our Servo-Electric Powder Presses
You can experience precise and accurate material formation with electric powder presses from Gasbarre. Our robust and reliable machines deliver countless functions that will serve your company for decades.
As a full-service international original equipment manufacturer (OEM) that customers trust, we always stay up-to-date with the latest technological advancements — so purchasing products through us means investing in modern, top-of-the-line equipment for your company.
Our Custom Electric Metal Press Capabilities
Our next-level fabrication capabilities allow us to offer electric press customization services to deliver solutions individualized to our customers’ needs. When you come to Gasbarre for custom presses, we’ll take the time to learn about your unique goals and objectives and determine the most efficient way to integrate our machines into your company’s processes. Then, we’ll use our expert fabrication skills to create your specialized system.
Advantages of Electric Powder Compaction Presses
When you invest in electric servo presses for your facility, you’ll experience all of the following benefits for your company:
- Energy efficiency
- Increased operator safety
- Reduced operational costs
- Fewer maintenance needs
- Leak-free operation
- Noise-free function
- Longer component life
Why Choose Gasbarre for Electric Powder Presses?
Gasbarre has delivered high-quality manufacturing equipment to industrial companies worldwide since founding our family-owned business in 1973. We care about our customers — that’s why we never discontinue equipment services to force individuals into buying our latest solutions. Rather, we service our machines to maximize service life.
Our team is dedicated to prioritizing our customers, meaning we’ll go above and beyond to serve you on weekends and holidays if necessary.
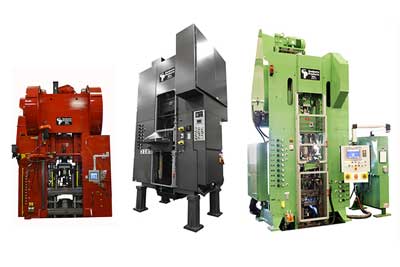
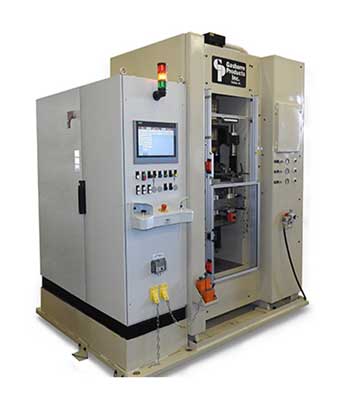
You are looking for Molding Bags and Sealing Membranes for your presses. Then we are the right partner for you. You can find more information here.
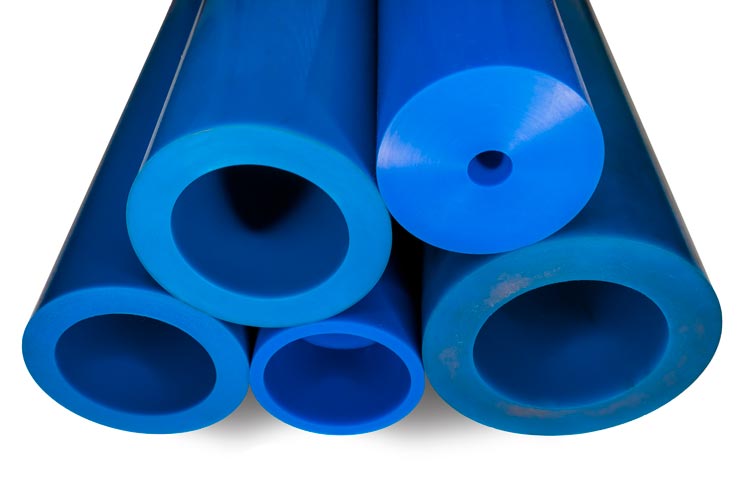
Thermal Processing Systems – Industrial Furnaces
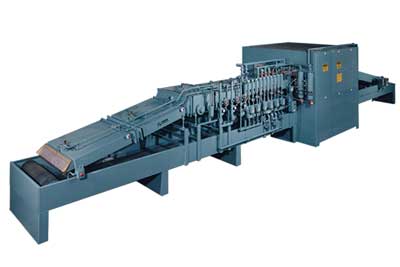
About
Gasbarre
Gasbarre, headquartered in DuBois, PA, was founded in 1973 to design, manufacture, and service a complete line of powder compaction and sizing presses for the powder metallurgy industry. Since that time, Gasbarre has earned a worldwide reputation as a full service supplier to the powder metallurgy, particulate materials and thermal processing industries.
With over 200 employees in seven locations, Gasbarre stands alone in the ability to offer equipment and services for all applications related to powder compaction and thermal processing. Today, with 20% of Gasbarre products being exported, there are thousands of Gasbarre presses, furnaces and other equipment in operation all around the globe.
Gasbarre Products, Inc.
DuBois, PA | USA
Established in 1973
ISO 9001 CERTIFIED
ISO 17025 CERTIFIED
JVS Sales & Technical Consultants GmbH
We are here for your ideas.
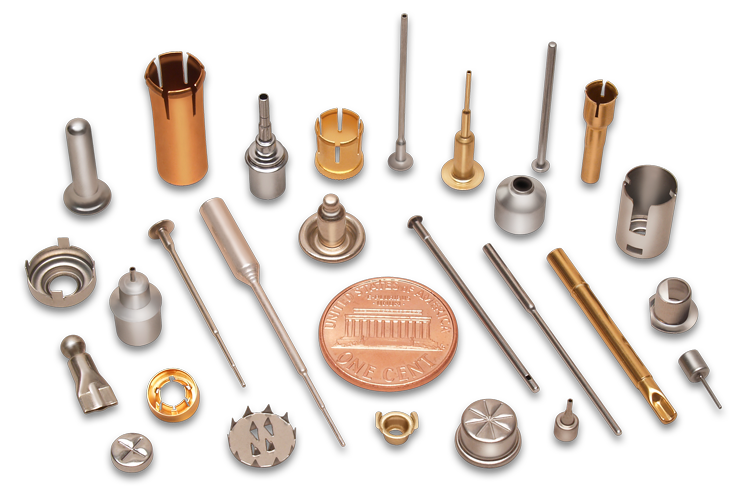
Deep Drawing
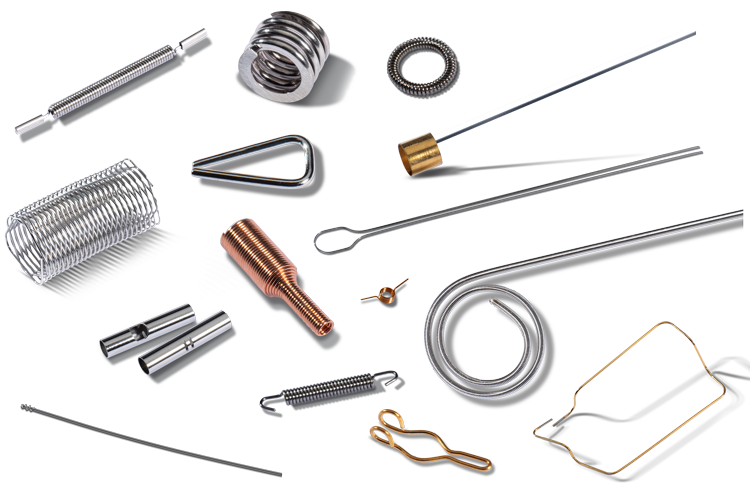
Micro Springs & Wire Forms
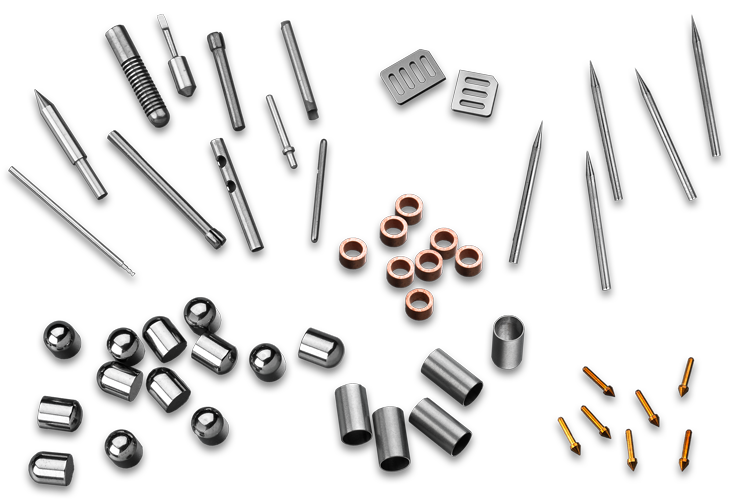
Metal Cutting
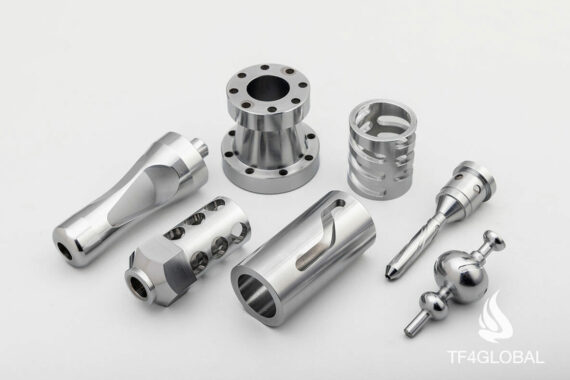
Machining
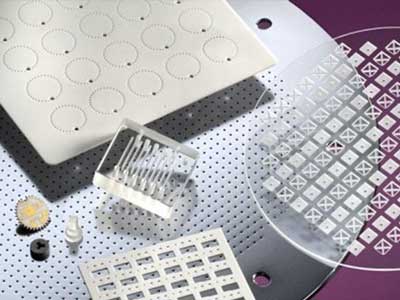
Ultrasonic Machining
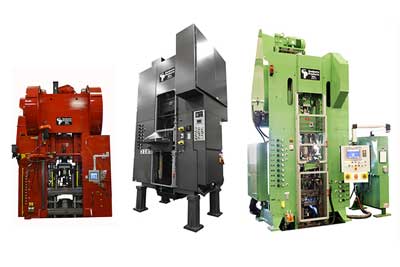
Powder Compaction
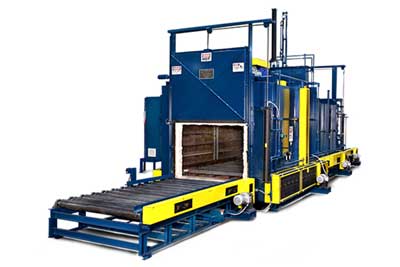
Thermal Processing
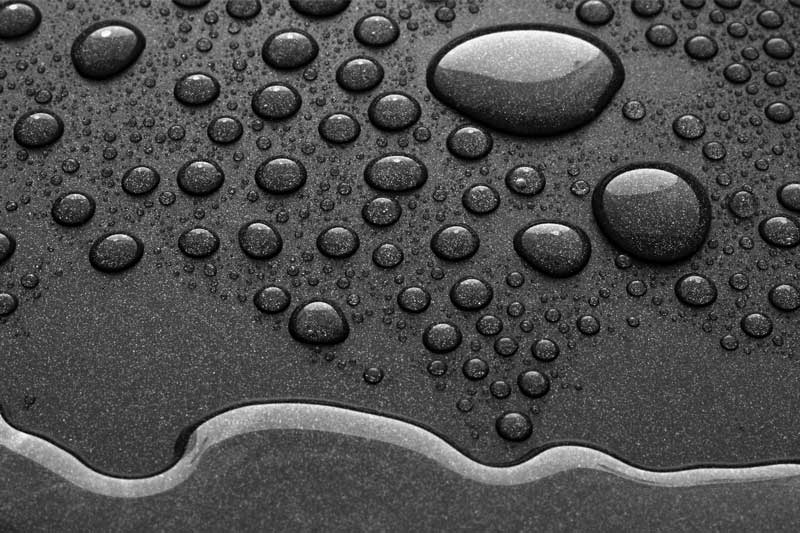
Surface Coatings
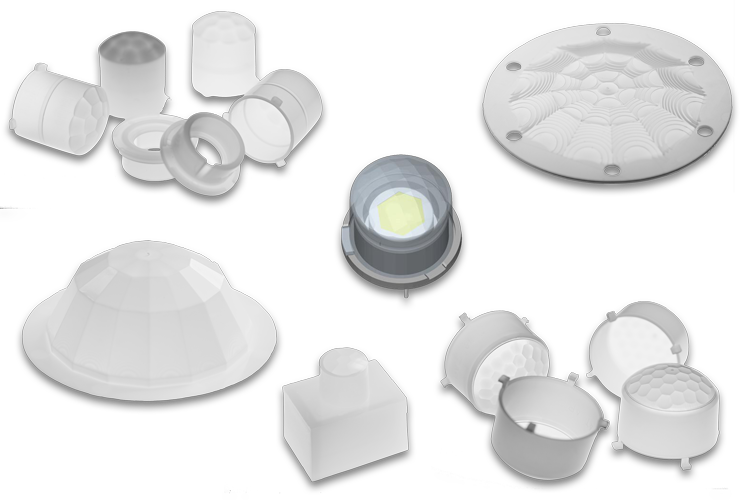
PIR Lens Solutions
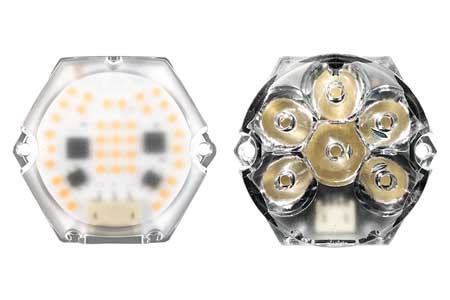